Introduction
In the world of material science, coating techniques play a pivotal role in determining the properties and performance of various materials. Two of the most prevalent techniques are evaporation and sputtering. Both methods have their unique advantages and disadvantages, and their suitability varies depending on the crystal materials in question.
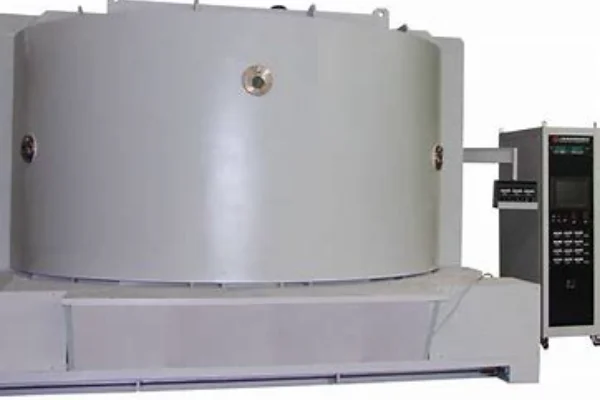
Understanding the Basics: What is Evaporation?
Understanding the intricacies of evaporation as a coating technique requires a deep dive into the physical vapor deposition (PVD) process. At its core, evaporation is a transformative process where a material transitions from a solid phase to a gaseous phase. This metamorphosis is not a random occurrence but a meticulously controlled process that takes place under vacuum conditions. The vacuum serves a dual purpose. Firstly, it creates an environment devoid of air and other gases, which could otherwise interfere with the vapor particles. Secondly, it provides the necessary conditions for the vapor particles to travel unimpeded directly to the target object.
The journey of the vapor particles doesn’t end upon reaching the target object. Instead, they undergo another transformation, condensing back into a solid form. This condensation results in the creation of a thin film on the target object. The thickness of this film can be controlled with precision, making evaporation a versatile technique for a variety of coating applications.
One of the primary advantages of evaporation is its simplicity. The process doesn’t require complex machinery or intricate procedures. This simplicity translates into cost-effectiveness, making evaporation a viable option for large-scale industrial applications where budget constraints are a significant consideration.
Another advantage of evaporation is the high purity of the coatings it produces. The vacuum conditions in which evaporation occurs minimize the risk of contamination from air and other gases. This results in coatings of exceptional purity, which is a critical factor in many applications, particularly in the electronics and aerospace industries where material purity can significantly impact performance.
Despite its numerous advantages, evaporation is not without its limitations. One of the primary challenges with this technique is its struggle with coating complex shapes uniformly. The process relies on a line-of-sight transfer of material from the source to the target. This means that any parts of the target object not directly in line with the source may not receive an even coating, limiting the technique’s effectiveness for objects with intricate shapes or recessed surfaces.
Another limitation of evaporation is its effectiveness with high melting point materials. These materials require a significant amount of energy to transition from a solid to a gaseous state. The energy requirements can increase the cost and complexity of the evaporation process, making it less suitable for such materials.
In conclusion, while evaporation as a coating technique offers several advantages, including simplicity, cost-effectiveness, and high purity coatings, it also has its limitations. Its struggle with coating complex shapes uniformly and its lessened effectiveness for high melting point materials are challenges that need to be considered when choosing a coating technique. Despite these limitations, evaporation remains a widely used and valuable tool in the material science toolbox.
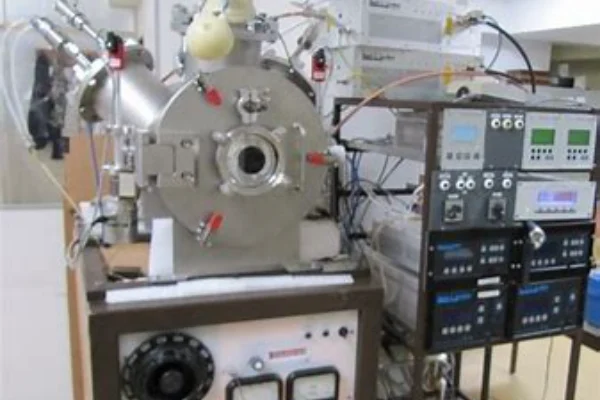
Diving Deeper: What is Sputtering?
Delving deeper into the realm of coating techniques, we encounter sputtering, another form of physical vapor deposition (PVD) process. While it shares the same overarching category with evaporation, the mechanics of sputtering are distinct. Instead of transitioning material from a solid phase to a gaseous phase, sputtering involves a more aggressive approach. The process is characterized by the ejection of material from a source, known as the “target,” onto a “substrate” or surface. This ejection is not a spontaneous event but is triggered by the bombardment of the target material with high-energy particles. These particles dislodge atoms from the target, which then travel through the vacuum to deposit on the substrate, forming a thin film.
One of the areas where sputtering truly shines is in its ability to coat complex shapes uniformly. Unlike evaporation, which struggles with this due to its line-of-sight nature, sputtering can effectively coat surfaces of any shape or size. This is because the ejected material can move in all directions, allowing it to reach and coat all areas of the substrate. This makes sputtering an ideal choice for coating objects with intricate geometries or recessed surfaces.
Another advantage of sputtering is its effectiveness with high melting point materials. While evaporation can struggle with these due to the high energy required to transition them into a gaseous state, sputtering has no such limitations. The high-energy particles used in sputtering can dislodge atoms from even the most stubborn of materials, making it a versatile technique for a wide range of applications.
Sputtering also allows for the deposition of multi-layer structures and alloys. This is a significant advantage as it expands the range of applications for the technique. With sputtering, it’s possible to create complex coatings with multiple layers, each with different properties. This opens up a world of possibilities in material design and engineering, allowing for the creation of materials with tailored properties to suit specific applications.
However, sputtering is not without its challenges. The process is more complex than evaporation, requiring more sophisticated equipment and a deeper understanding of the underlying physics. This complexity also translates into higher costs, making sputtering a more expensive option compared to evaporation.
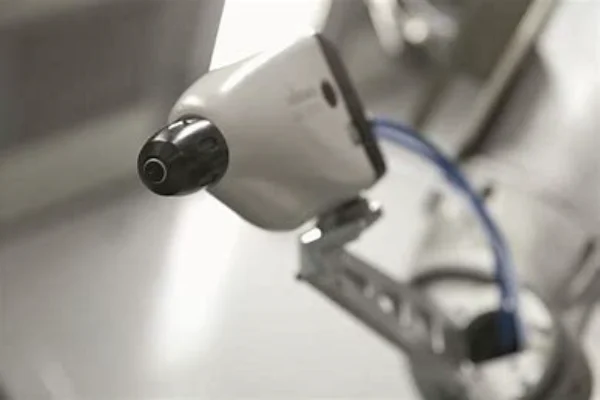
Another challenge with sputtering is the need for precise control over process parameters. Factors such as the energy of the bombarding particles, the pressure in the vacuum chamber, and the composition of the target material all need to be carefully controlled to ensure the quality of the coating. Any deviations can result in coatings with sub-optimal properties, making the process less forgiving than evaporation.
In conclusion, sputtering is a powerful coating technique that offers several advantages over evaporation, including the ability to coat complex shapes uniformly, effectiveness with high melting point materials, and the ability to deposit multi-layer structures and alloys. However, these advantages come with their own set of challenges, including higher complexity and cost, and the need for precise control over process parameters. Despite these challenges, sputtering remains a valuable tool in the material science toolbox, offering unique capabilities that make it an essential technique in many applications.
Evaporation vs. Sputtering: A Comparative Analysis
In the realm of coating techniques, evaporation and sputtering stand out as two of the most commonly used methods. Each has its unique strengths and weaknesses, and the choice between the two often comes down to the specific requirements of the application at hand.
Evaporation, with its simplicity and cost-effectiveness, often emerges as the go-to choice for applications where budget constraints are a significant factor. The process is straightforward and doesn’t require complex machinery or intricate procedures, making it a cost-effective solution for large-scale industrial applications. Moreover, evaporation excels in producing high purity coatings. The vacuum conditions under which evaporation occurs minimize the risk of contamination from air and other gases, resulting in exceptionally pure coatings. This is a critical factor in many applications, particularly in industries like electronics and aerospace, where material purity can significantly impact performance.
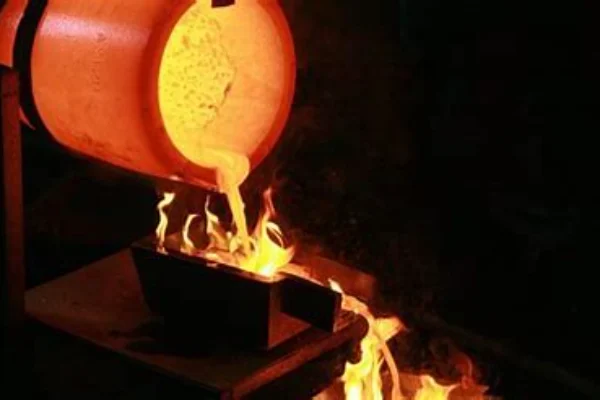
On the other hand, sputtering is often the preferred choice when versatility is a key requirement. Unlike evaporation, sputtering can effectively coat surfaces of any shape or size, making it ideal for objects with intricate geometries or recessed surfaces. Furthermore, sputtering is effective with high melting point materials. The high-energy particles used in sputtering can dislodge atoms from even the most stubborn of materials, making it a versatile technique for a wide range of applications.
In conclusion, both evaporation and sputtering have their unique strengths and are suited to different applications. The choice between the two ultimately comes down to the specific requirements of the application, with evaporation being the more cost-effective and purity-focused option, and sputtering offering greater versatility and effectiveness with complex shapes and high melting point materials.
Suitability for Different Crystal Materials
The choice between evaporation and sputtering also depends on the crystal material being coated. For instance, organic crystals that are sensitive to high energy may be better suited to evaporation. On the other hand, inorganic crystals that can withstand high energy conditions may benefit more from sputtering.
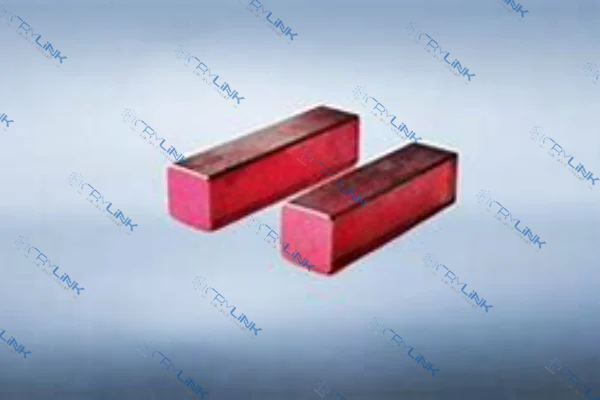
Conclusion
In conclusion, both evaporation and sputtering have their unique strengths and weaknesses. The choice between the two ultimately depends on the specific requirements of the application and the nature of the crystal material being coated. By understanding these factors, one can make an informed decision that optimizes the performance and efficiency of the coating process.
FAQs
- What is the main difference between evaporation and sputtering?
- The main difference lies in the process. Evaporation involves transitioning a material from a solid to a gas phase, while sputtering involves ejecting material from a target source onto a surface.
- Which coating technique is more cost-effective?
- Evaporation is generally more cost-effective due to its simplicity and lower energy requirements.
- Can both techniques be used for any crystal material?
- The suitability of the techniques varies depending on the crystal material. Some materials may be better suited to evaporation, while others may benefit more from sputtering.
- Which technique is better for high melting point materials?
- Sputtering is typically more effective for high melting point materials as it can operate at higher energy levels.
- Can both techniques achieve high purity coatings?
- Both techniques can achieve high purity coatings, but evaporation has an edge due to the vacuum conditions that minimize contamination.